Die Casting Mold Design: Essentials for Precision and Efficiency
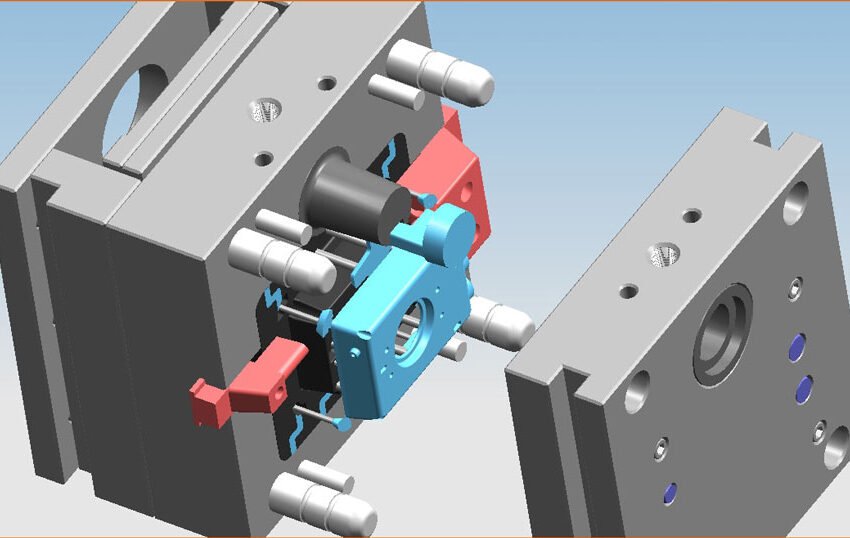
Fundamentals of Die Casting Mold Design
In this section, you will learn about the key principles that guide mold design, a brief look at the die casting process, and the various types of molds used in die casting.
Key Principles of Mold Design
When creating a die-casting mold, certain principles are essential. First, consider the shrinkage of metal. As molten metal cools, it shrinks. You need to account for this to maintain accuracy.
Next, design for ease of ejection. Molds should allow for smooth removal of the cast part without damage. This often involves using draft angles, which are slight slopes that help parts come out easily.
Lastly, think about venting. Proper vents release gases that escape during the casting process. If not designed well, trapped air can create defects.
Die Casting Process Overview
The die casting process begins with melting metal, usually aluminum or zinc. Once melted, the metal is injected into the mold under high pressure. This ensures the metal fills every corner.
After injection, the metal cools and solidifies in the mold. This cooling time depends on the thickness of the part and the material used.
Finally, the mold opens, and the part is ejected. This setup allows for rapid production of precise parts, making die casting a popular choice for many industries.
Types of Die Casting Molds
There are two main types of die-casting molds: permanent molds and sand molds.
- Permanent moldsare made of metal and can be reused many times, making them ideal for high-volume production.
- Sand molds:These are used for lower production runs and are made from a mixture of sand and binder. They are less expensive but only last for a few cycles.
Additionally, molds can be classified based on their design. For instance, single-cavity molds produce one part per cycle, while multi-cavity molds create several parts at once, optimizing efficiency. Understanding your project’s needs will help determine the best mold type.
Material Selection for Die Casting Molds
Choosing the right materials for your die casting molds is crucial for their performance and longevity. You’ll find that different alloys have unique properties, and understanding these will help you make better decisions for your projects.
Common Alloys Used in Die Casting
Die casting commonly uses several types of alloys. The most popular choices include:
- Aluminum Alloy: Known for its good casting characteristics, aluminum alloys provide excellent strength and lightweight properties. They work well in various applications.
- Zinc Alloy: Zinc alloys have great fluidity, which helps in producing intricate shapes. They also offer good corrosion resistance and are cost-effective.
- Magnesium Alloy: This alloy is lightweight and has high strength-to-weight ratios. It is ideal for applications where minimizing weight is essential.
These alloys are preferred due to their balance of strength, weight, and cost efficiency.
Mold Material Considerations
When selecting mold materials, you need to think about several factors:
- Tool Steel: Tool steels are often used for their hardness and durability. They withstand high temperatures and pressures, making them ideal for die casting.
- Aluminum Alloys: Lightweight and easy to machine, aluminum molds are suitable for shorter production runs. They can be less expensive but might wear out faster.
- Copper Alloys: Copper molds are excellent at conducting heat. This helps reduce cycle times but can be more costly than other options.
Evaluating the project’s specific requirements will guide you in choosing the best material.
Corrosion Resistance and Mold Durability
Corrosion resistance is important for mold longevity. A durable mold can save you money and time in the long run. Here are some points to consider:
- Protective Coatings: Adding a protective coating to your mold can increase resistance to corrosion. This helps extend the service life of your mold.
- Material Selection: Choosing alloys with inherent corrosion resistance, like zinc, can further enhance durability. It’s essential for molds exposed to moisture or harsh environments.
- Maintenance: Regular maintenance can prevent corrosion and improve the lifespan of molds. Simple cleaning routines can greatly impact performance.
By paying attention to these factors, you can ensure that your molds perform effectively over time.
Mold Structure and Components
Understanding the structure and components of a die casting mold is essential for successful design. Key elements include mechanisms for pulling cores, surfaces that help with alignment, and systems for ejecting parts from the mold.
Core Pulling Mechanisms
Core pulling mechanisms are used to remove interior shapes from cast parts. These often include mechanical devices that operate during the mold opening.
- Types of mechanisms: Common types are hydraulic, pneumatic, and manual systems.
- Functionality: They work by applying force to pull the core out after the metal has cooled and solidified.
- Benefits: Using a core pulling mechanism allows for complex shapes and improves the quality of the final part.
Parting Surfaces and Guide Posts
Parting surfaces are where the two halves of the mold meet. They are critical for ensuring a tight fit during casting.
- Guide Posts: These components help align the mold halves. They ensure that both parts come together correctly.
- Importance: Proper alignment prevents leaks and defects in the casting. The smoother the parting surfaces, the less finishing work needed later.
Ejection Systems and Sliders
Ejection systems are crucial for removing the finished part from the mold. Without them, the casting would remain stuck, causing damage.
- Ejector Pins: These pins push the cast part out of the mold when it opens. They can be single pins or a series of them.
- Sliders: Sliders are used for complex shapes that require additional movement during ejection. They allow parts with undercuts to be released easily.
Fixed and Movable Mold Elements
Mold elements can be classified into fixed and movable parts. Each plays a distinct role in the casting process.
- Fixed Mold Elements: These parts remain stationary during casting and are responsible for containing the molten metal. They form the main shape of the part.
- Movable Mold Elements: These parts can shift to help with core pulling or ejection. They allow for flexibility in design and can create more intricate shapes.
Understanding these components helps you design more effective molds. Each part contributes to the overall efficiency and quality of the die casting process.
Design Considerations for Die Casting Molds
When designing die casting molds, specific factors play a crucial role in ensuring quality and efficiency. Key aspects include wall thickness, the use of casting fillets and rounded corners, as well as ensuring strength and rigidity in the mold structure. It’s also important to reduce stress concentration to prevent defects.
Wall Thickness Design
Wall thickness is vital in die casting. Thin walls can cause issues like warping or cracking during cooling. Aim for a uniform thickness of about 2 to 6 mm for most parts. This range helps maintain strength while allowing for efficient material use.
You should also consider how the part will be ejected from the mold. If walls are too thick, it may be challenging to release the part. Using draft angles can help with the ejection, making the process smoother.
Casting Fillets and Rounded Corners
Using casting fillets and rounded corners helps reduce sharp angles that could lead to stress concentration. These features allow for better material flow during the casting process. For example, fillets can lower the risk of defects and improve the mold’s durability.
Optimal radii for these features depend on the part’s design and size. Common practice is to use radii that are at least 10% of the wall thickness. This guideline helps maintain a strong structure while making it easier for the casting material to fill the mold.
Strength and Rigidity
Strength and rigidity are crucial for die casting molds. When the mold is under pressure, it must hold its shape to avoid deformities in the cast part. Using high-strength materials like steel or aluminum alloys is recommended for better durability.
It’s important to design the mold to prevent deflection. Adding support structures or ribs can increase rigidity without adding excessive weight. This can help you create molds that last longer and produce high-quality parts consistently.
Stress Concentration Reduction
Reducing stress concentration is key in mold design. Sharp corners and sudden changes in wall thickness can lead to weak points. Implementing gradual transitions and smooth curves helps distribute stress evenly across the part.
Consider using tools like finite element analysis (FEA) during the design phase. FEA can predict where stress will accumulate, allowing you to make adjustments before physically creating the mold. This proactive approach can save time and material while preventing defects in the final product.